Tutorial 8 - Multi-Component Flow
The files for this tutorial can be found in “examples/tutorial_8”.
Governing Equations
This tutorial will demonstrate how to add convection, diffusion, and reaction of multiple dissolved components to incompressible Navier-Stokes flow. The test case will be a channel containing multiple circular catalyst particles at whose surface component A undergoes a first-order irreversible reaction to transform into component B. The reaction and transport of components A and B are modelled by the following equations:
The velocity profile comes from the solution of the incompressible Navier-Stokes equations, given below with Oseen-style linearization:
with a kinematic viscosity of 0.001.
The Main Configuration Files
The main configuration file is very similar to that used in Tutorial 7 - IMEX Schemes.
One major change is the addition of finite element spaces for components A and B. Note that the discontinuous Galerkin method is not used as it is not yet fully implemented for multi-component flows. Instead, the Taylor-Hood finite element pair is used for velocity and pressure and the additional components use the same scalar finite elements as the pressure field.
[FINITE ELEMENT SPACE]
elements = u -> VectorH1
p -> H1
a -> H1
b -> H1
interpolant_order = 3
[DG]
DG = False
The transient solve parameters should also be modified to increase the simulation duration and ensure a steady flow is eventually achieved.
[TRANSIENT]
transient = True
scheme = implicit euler
time_range = 0.0, 10.0
dt = 1e-2
Finally, the model type must be changed to “MultiComponentINS” and the model must be given information about the additional components. The components must be named according to how they are referenced in the configuration files and it must be noted that the component results should be used in any error calculations and that the governing equations for both components include time derivative terms.
[OTHER]
model = MultiComponentINS
component_names = a, b
component_in_error_calc = a -> True
b -> True
component_in_time_deriv = a -> True
b -> True
run_dir = .
num_threads = 2
The Boundary Condition Configuration File
The boundary condition configuration file now must include boundary conditions for component transport and reaction in addition to the usual flow boundary conditions.
[DIRICHLET]
u = inlet -> [y*(0.5-y)/0.5^2, 0.0]
wall -> [0.0, 0.0]
circle -> [0.0, 0.0]
a = inlet -> 1.0
b = inlet -> 0.0
[STRESS]
stress = outlet -> [0.0, 0.0]
[TOTAL_FLUX]
a = outlet -> 0.0
wall -> 0.0
b = outlet -> 0.0
wall -> 0.0
[SURFACE_RXN]
a = circle -> -a
b = circle -> a
Note that the surfaces of the catalyst particles have been marked “circle” on the mesh.
The Initial Condition Configuration File
The initial conditions are simply zero throughout the domain.
[MultiComponentINS]
u = all -> [0.0, 0.0]
p = all -> 0.0
a = all -> 0.0
b = all -> 0.0
The Model Configuration File
The model configuration file contains the usual model parameters and model functions for the flow distribution and now additional ones for component transport.
[PARAMETERS]
kinematic_viscosity = all -> 1
diffusion_coefficients = a -> 1
b -> 1
[FUNCTIONS]
source = u -> [0.0, 0.0]
a -> 0
b -> 0
The Error Analysis Subdirectory
In this case, the exact solution is not known, so the error analysis configuration file is left empty. Note that the divergence of the velocity and the velocity could be calculated – it doesn’t require a reference solution – but aren’t.
Running the Simulation
The simulation can be run from the command line; within the directory “examples/tutorial_8/” execute python3 -m opencmp config
.
As usual, the progress of the transient simulation can be tracked from the print outs at each time step. Once the simulation has finished the results can be visualized by opening “output/transient.pvd” in ParaView. Below is the distribution of components A and B after 10s:
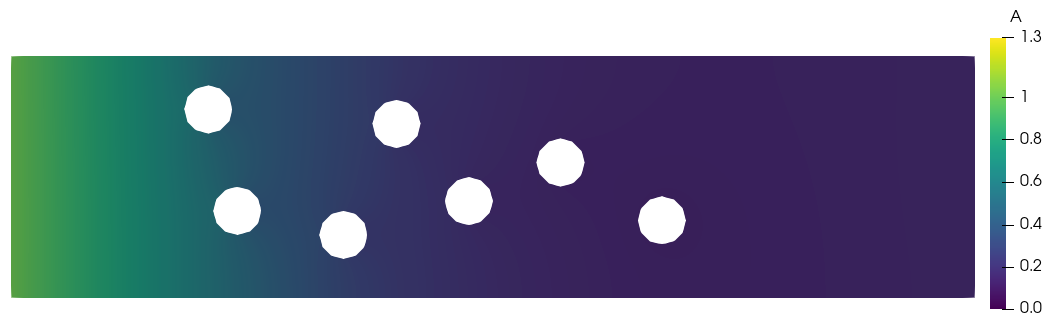
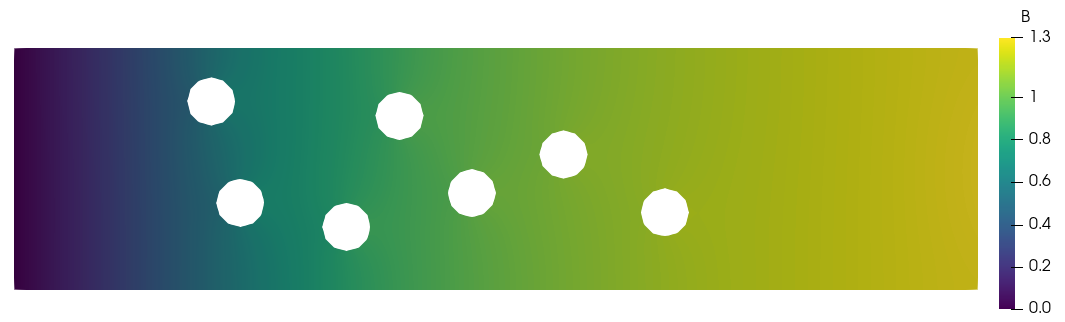
and the velocity and pressure distributions:
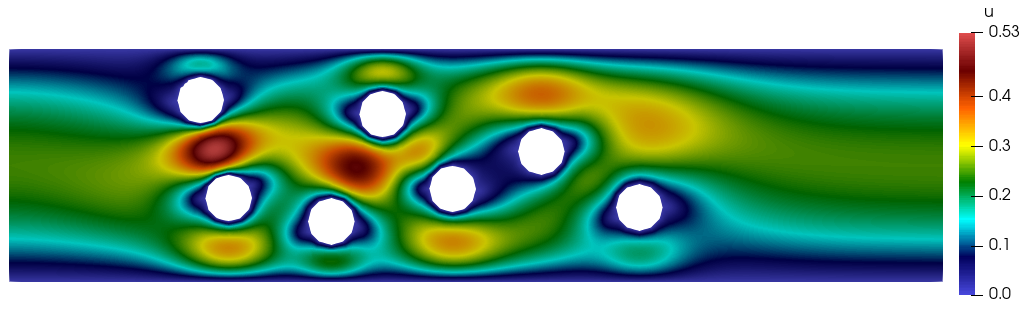
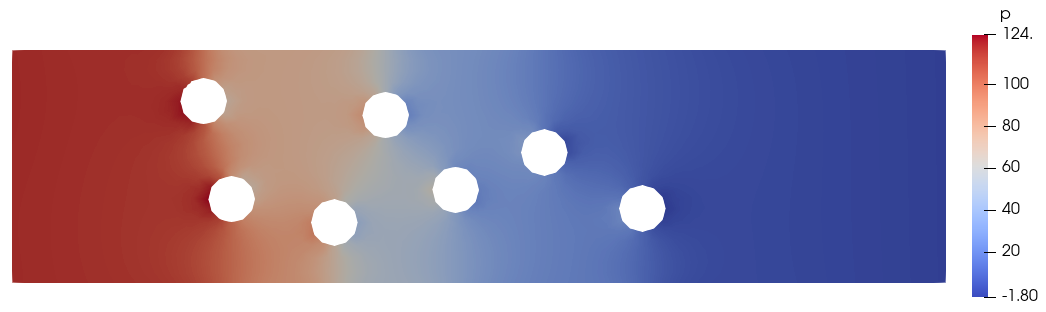